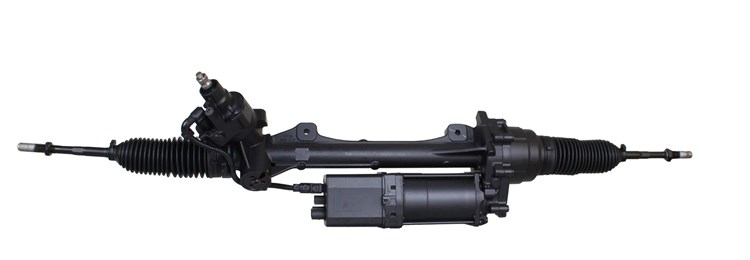
Shaftec explains how FlexRay works to keep pace with automotive advances
Date: Friday 12 May 2023
At Shaftec, we firmly believe that to ensure a growing and sustainable independent aftermarket, knowledge is power, education is key and investment in R&D paramount. In 2023 technology continues to advance at pace. This not only concerns the vehicles and powertrains, but also the aftermarket parts themselves which must be adapted to meet the ever-changing communication needs of a world striving for continuously improved automotive performance. Here, the business looks at the next generation automotive communication protocol FlexRay and how it is used by Shaftec to future proof its parts and benefit its customers.
Flexray is an electrical communication technology that is used to enable high-speed and fault tolerant data exchange between different electronic control units (ECUs) in a vehicle. Like most things in the automotive world, it is an evolution not a revolution and has evolved so that parts can synchronize to share data and communicate with the vehicle, delivering high end performance.
CAN (Controller Area Network) is currently used in most vehicles on the roads today, and in the past, this provided a powerful enough ‘bandwidth’ for the parts and vehicle to communicate. As technology has progressed, however, and more VMs have moved over to FlexRay which allows intercommunication of all electronic parts via the cars own mini ‘ethernet’, CAN FD (Flexible Data Rate) was introduced to try and bridge the gap. The aim of each protocol is to provide a connection between the components and the vehicle, so everything works in tandem.
To aid understanding, it helps to view the evolution of moving from CAN through to FlexRay is a bit like going from a dial up connection to fibre:
- CAN could be compared to an old Dial Up connection or 3G. With a low data transfer rate of up to 1Mbps, it can be unstable, unreliable and moves data slowly.
- CAN FD can be viewed as the next step-up, Broadband or 4G, which is better, more reliable, and stable and moves data faster. With data transfer speeds of up to 8Mbps it provides more flexible data frame formats allowing more efficient use of the available bandwidth. From a technical viewpoint, CAN FD allows for data frames of 64 bytes compared to the 8 bytes limit of CAN which reduces the number of messages.
And then there’s FlexRay, which is akin to Fibre Optic Broadband or 5G. With a data transfer rate of 10 Mbps, it’s far more stable and reliable and moves data much faster. This greater bandwidth results in greater control over safety systems and management of all components which is paramount with the constant expanding technologies in cars and their components. FlexRay also offers built in redundancy, meaning it can use two separate communication channels to transmit data. If one channel fails, the other channel can continue to transmit data. CAN does not have this functionality. Considering this, CAN is generally less expensive than FlexRay, making it a more cost-effective solution where high speed and synchronisation are not required.
- Introduced in 2008 (and patented by a major VM), FlexRay was explicitly designed to meet the demands and challenges of the drive-by-wire (start-by-wire, brake-by-wire) and advanced device assistance systems (engine, transmission). The protocol has advanced to now offer reliable and fast communication for advanced safety systems, such as Antilock Braking (ABS), Electronic Stability Control (ESC), and Adaptive Cruise Control (ACC).
Designed for high determinism (guarantee that data will be transmitted within a specific time window) FlexRay uses a time-triggered protocol to ensure that all ECUs receive information at the same time and synchronises communication makes FlexRay important in safety critical applications where timing is critical, such as Advanced driver Assistance Systems (ADAS) and Autonomous Driving. Another example is where FlexRay protocols are used to send data from the steering wheel angle sensor to the ESC system to assist with vehicle stability.
“With vehicle manufacturers using this technology on an increasing number of vehicles, at Shaftec we’ve long understood that aftermarket growth was inevitable,” explains Andrew Ferber, Operations Manager, Shaftec.
“We’ve been working on this project for many years which has required a massive amount of work into R&D as well as greatly expanding the physical space being used within our facility to accommodate for the differing technologies in steering. We made the decision not to use the bridging technology protocol, CAN FD, but rather went straight to FlexRay as CAN FD is not reversely compatible with traditional CAN systems. Where the two need to be used in the same system, a protocol converter needs to be used. Now, at Shaftec, we can read Electrical Steering Racks and Electrical Steering Pumps when they come in – as core or as a surcharge unit in return - before the remanufacturing process starts, and ensure the finished, fully remanufactured parts are compliant and able to use FlexRay communication technology when they leave us, enabling reliable fitment without coming into electronic blockers.”
The Shaftec FlexRay Process
- The core unit is visually inspected, checked for conformity to criteria and ID matched to OE numbers, manufacture dates and casting numbers.
- It is then connected to the test bench and powered up to establish communications.
- An automotive diagnostics tool is connected.
- The unit will be then have operational parameters and the following internal information checked: voltages, amps, speed sensor type and functionality, torque sensor functionality, vehicle speed, position sensors, angle sensors, codings, software ID, hardware ID, diagnostics and if present, all trouble Codes (DTC) are retrieved to assess the reasons why it was removed and to determine if a repair is required or not.